Notre équipe
VOTRE SUCCÈS EST AUSSI LE NÔTRE
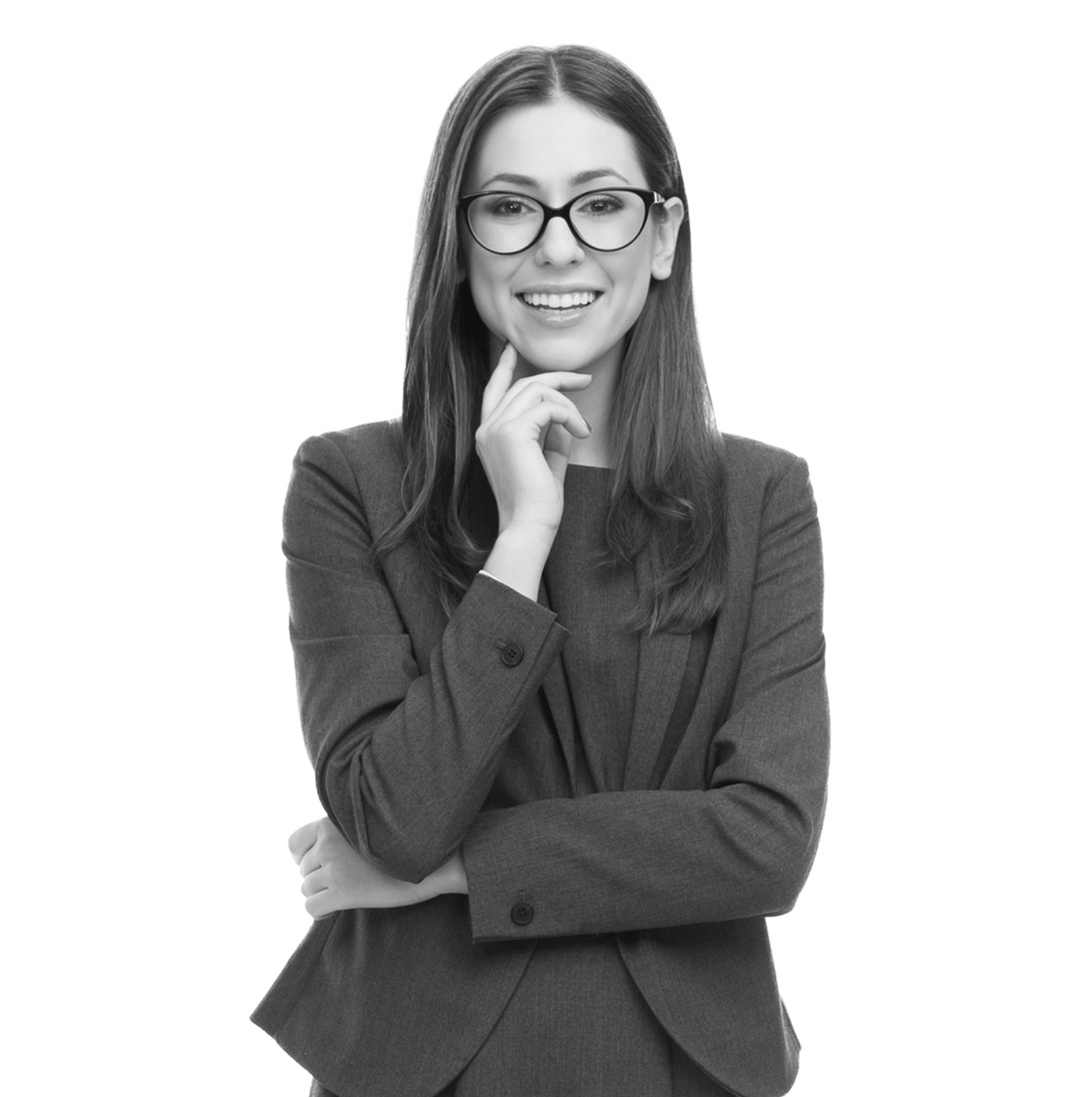
The Benefits of Laser Welding
Many parts in the manufacture of automobiles need to be welded. Welding is an important part of auto parts, so the quality of welding is very important. There are many welding methods for auto welding, but laser welding is directly reduced by a higher welding process. The weight of the car body, the assembly precision of the car body, and the rigidity of the car are greatly reduced, the cost of the car body and the accessories in the manufacturing process is greatly reduced, and the cost of the whole car is reduced. Therefore, the green laser pointer welding machine for the auto parts welding is a better choice.
With the development of laser technology, the reliability of laser welding equipment is improved, manufacturers no longer worry that laser welding equipment will affect the normal operation of the production line. Currently, laser equipment equipped on the automobile production line can run continuously for 24 hours, and the failure rate is very high. low. Modular design is now used, maintenance is also very convenient, technical requirements for maintenance personnel are not high, and repair time is very short. Due to the high-speed continuous operation of the laser welding equipment, the investment recovery time of the laser welding equipment is shortened, which not only improves the productivity, but also improves the quality of the automobile. The laser technology will also bring great economic and social benefits.
Laser welding is the most widely used laser welding technology in the automotive industry, as well as 488nm laser pointer marking technology and laser cutting technology. Laser welding uses a high-energy-density laser to illuminate the material connection at a material source, so that the separated material absorbs the laser energy and then rapidly melts or vaporizes and forms a molten pool together, which solidifies together and then joins together in the subsequent cooling process. There are two common types of high-power lasers for laser welding: CO2 lasers and solid/fiber lasers. The former has a wavelength of 10.6 μm or a wavelength of 1.06/1.07 μm, which is invisible to the naked eye.
The automotive industry uses a large number of laser-welded steel sheets and unequal-thickness steel plates to make full use of the excellent properties of laser welds. After welding, it is stamped and formed without cracking. On the one hand, for the steel parts with insufficient width, the parts of the car body are welded after welding, because the different parts of the car body are different in force, and the requirements on strength and rigidity are also different. In order to reduce the weight of the car body, the thickness is often selected according to the actual needs of each part. Different types of steel or different surface treatment methods are laser welded together as a blank before stamping. Compared with the old process, the integration of a plurality of punching sheets reduces many punches, so that not only the weight of the vehicle body is reduced, but also the cost is lowered. In addition, bumpers, body frames, and ribbed parts can be used to replace the old process.
The common welding principle is actually liquefying the metal, then cooling it and then dissolving it together. The body of the car is welded by four steel plates from top to bottom and left and right. The ordinary welding is spot welding, and the steel plates are connected together by one welding point. Laser welding is the physical principle of using the high temperature of the waterproof laser pointer, disrupting the molecular structure of the two steel plates, and rearranging the molecules to dissolve the molecules in the two steel plates. The actual operation is to use a polarizer to reflect the laser beam, so that it concentrates on the beam that produces great energy from the focusing device. The laser beam has a diameter in the range of 0.2-0.6 mm at the focus point, and a light intensity exceeding 106-108 watts/cm 2 is obtained, the focus is close to the workpiece, and the surface of the workpiece reaches a physical change of the fusion bond. Therefore, laser welding turns two steel sheets into one steel sheet, so it has higher strength than ordinary welding.
In the manufacturing process, the car has high precision, high deformation, small heat, small flaws, high weld quality, no solder, high efficiency welding speed and welding quality, ensuring low cost operation and unconditional high feasibility in the car. In the industry, the welding of welded parts, the welding of the body parts and the welding of parts are realized.
Auto parts can reduce the number of parts and molds by military laser pointer welding, reduce the number of spot welds, optimize the amount of materials, reduce the weight of parts, reduce the cost and improve the dimensional accuracy. The strength of the steel plate after laser welding will increase by more than 30%; The width of the joint surface can be reduced, the use of the sheet material is reduced, and the rigidity of the vehicle body is improved; the welded parts of the automobile itself are free from deformation, the welding speed is fast, and the welding machine does not require heat treatment, and the flexibility is strong. The advantages of high-strength weld bead strength and high speed are realized.
Although the strength of the resistance spot welding head is better than laser welding, it is still higher than the metal base material. The weakest part of the overall welded body is the welding heat affected zone on the base metal. That is to say, the metal base material is the weakest link, so once the body is subjected to strong external force, in most cases, the metal base material is destroyed, not the welded joint. It is precisely because of the existence of the short plate of the metal base material that the strength of the laser welded body and the resistance spot welded body is almost indistinguishable. Therefore, the usb laser pointer welded body is not more safe than the resistance spot welding body when it is affected by external force.
Jules Bertrand
Directeur
Jules est chef d'équipe. Il est responsable de toutes les décisions finales. Porro quisquam est qui dolorem ipsum quia dolor sit amet consectetur adipisci velit sed quia non numquam eius modi tempora incidunt ut labore et dolore magnam aliquam quaerat voluptatem ut enim ad minima veniam quis nostrum exercitationem ullam corporis suscipit laboriosam nisi ut aliquid ex.
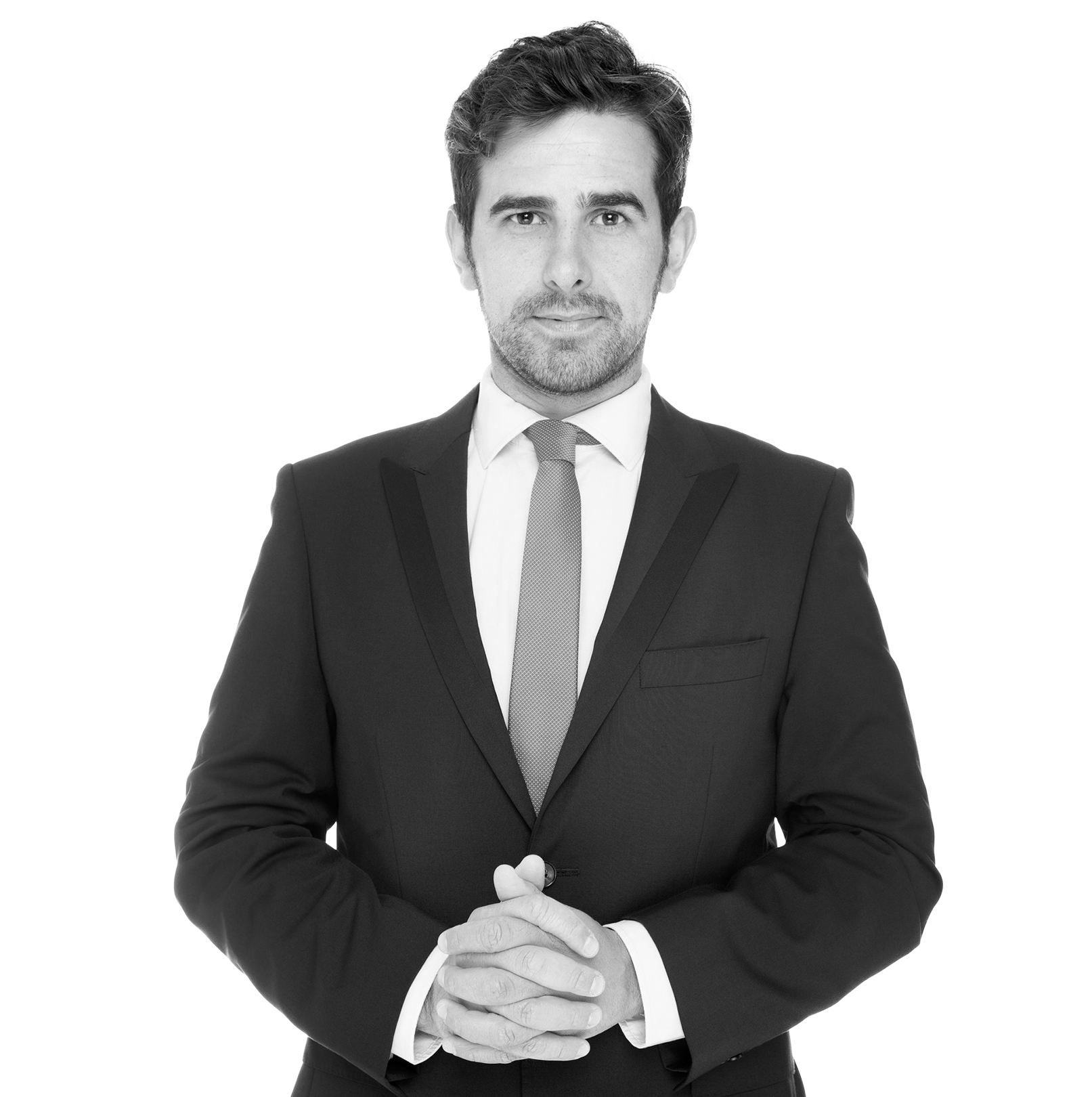
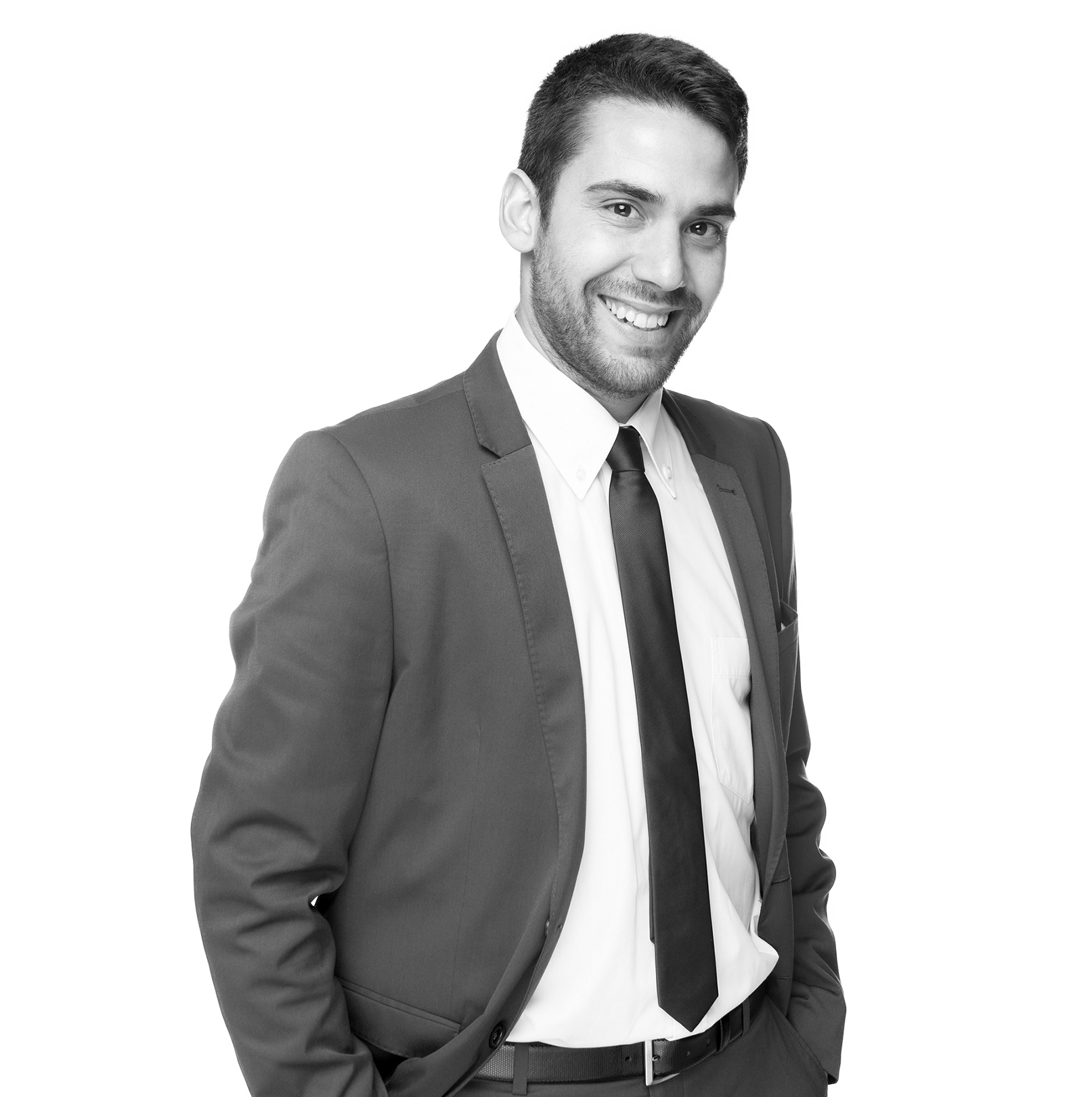
Guillaume Durand
PDG
Guillaume est l'un des fondateurs de notre bureau fiscal. Ea voluptate velit esse quam nihil molestiae consequatur vel illum qui dolorem eum fugiat quo voluptas nulla pariatur at vero eos et accusamus et iusto odio dignissimos ducimus qui blanditiis praesentium voluptatum deleniti atque corrupti quos dolores et quas molestias excepturi sint occaecati cupiditate non.